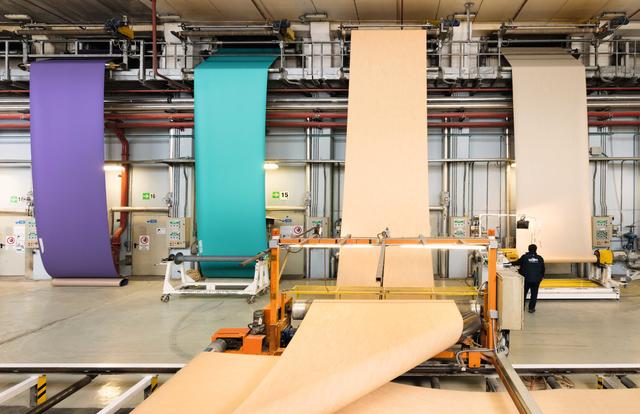
Nachhaltige Linoleum Herstellung - weniger CO2, gute Materialien und Recycling
Der Klimawandel ist die größte Herausforderung, vor der die Menschheit heute steht. Europa hat das Ziel bis 2050 klimaneutral zu werden und die Treibhausgasemissionen (THG) um 50-55 % zu senken. Die Kreislaufwirtschaft wird ein wichtiger Teil der Lösung sein, da 67 % der globalen Treibhausgasemissionen aus der Gewinnung, Verarbeitung und Herstellung von Gütern stammen. Daher ist die Umstellung auf eine effizientere und regenerative Produktion von entscheidender Bedeutung.
Wir bei Tarkett sehen in der Kreislaufwirtschaft die beste Möglichkeit, unsere CO2-Auswirkungen zu verringern und den Klimawandel zu bekämpfen. Daher arbeiten wir kontinuierlich daran, jede Lebenszyklus-Phase unserer Produkte zu verbessern. Indem wir Abfall und Umweltverschmutzung vermeiden, unsere Materialien optimieren, eine sauberere Produktion fördern und Produkte und Materialien wiederverwerten.
Das Innere unserer Linoleumfabrik in Narni
Unsere Linoleumfabrik in Narni, Italien, ist ein Paradebeispiel für nachhaltige Herstellung. Dort stellen wir zu 100 % recycelbares Linoleum her, das zu 94 % aus natürlichen Inhaltsstoffen besteht, die entweder erneuerbar oder in der Natur reichlich vorhanden sind. Darunter Leinöl, Kiefernharz, Holz- und Korkmehl, Kalziumkarbonat und Jute. Durch eine nachhaltige, energieeffiziente Produktion, die Vermeidung von Industrieabfällen und vor allem durch die Wiederverwertung von Linoleum zu neuen Linoleumböden verringern wir unsere Auswirkungen auf das Klima.
Durch die Gesamtwirkung all unserer Initiativen zur Verringerung des CO2-Ausstoßes in Narni konnten wir die Emissionen des Standorts seit 2010 um 60 % senken. Wir sind der einzige Bodenbelagshersteller, der die ISO14067-Zertifizierung erhalten hat, die unsere Fortschritte bei der Reduzierung der CO2-Emissionen bestätigt.
Wie gehen wir also mit unseren direkten und indirekten CO2-Emissionen um?
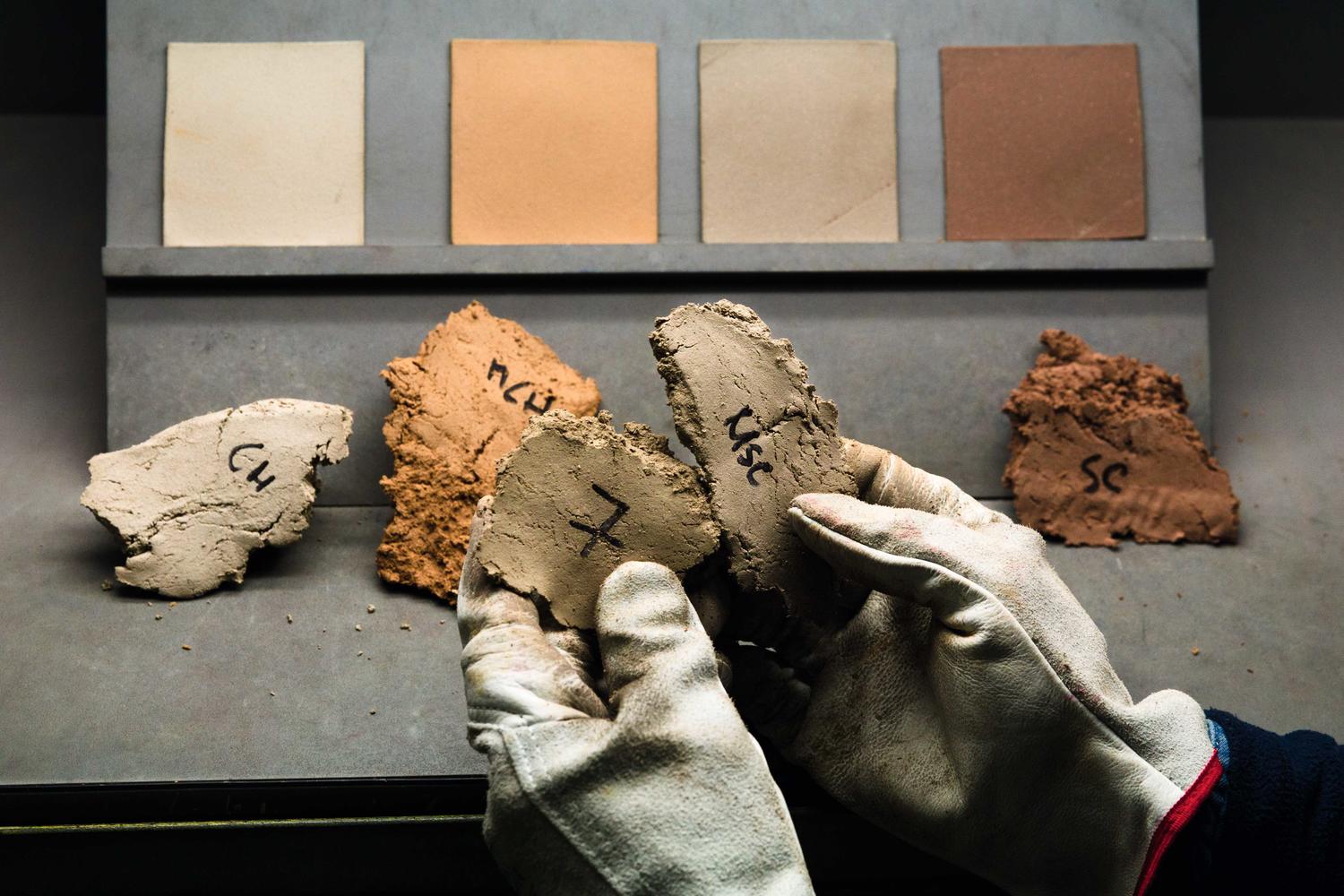
Schritt 1 - Emissionen: Verbesserung der Energieeffizienz
Wir verbessern die Energie- und Betriebseffizienz in unserem Werk in Narni, indem wir die energieintensivsten Maschinen und Anlagen sowie die mit der größten CO2-Belastung ermitteln. Dadurch konnten wir den Energiebedarf des Produktionsprozesses im Jahr 2019 gegenüber 2010 um 16,8 % senken. In ähnlicher Weise verbessern wir kontinuierlich die Wärmedämmung unserer Produktionsgebäude und -anlagen, um die Wärme zu speichern und unseren Energiebedarf zu senken. Außerdem haben wir ein geothermisches System mit niedriger Enthalpie in die bestehende Heiz- und Kühlanlage des Bürogebäudes integriert, wodurch der jährliche Gasverbrauch um -61 806 m³ und die CO2-Emissionen um -124 Tonnen gesenkt werden.
Schritt 2 - Emissionen: Nutzung erneuerbarer Energien
Wir verwenden zu 100 % Strom aus erneuerbaren Energien und erzeugen 34 % des Energiebedarfs unseres Werks in Narni vor Ort. Erreicht wird dies durch eine Kombination aus Wärmerückgewinnung (wodurch unser jährlicher Gasverbrauch um -804.782 m³ gesenkt wird), unserem Biomassekessel (wodurch unser Ofengasverbrauch um -347.000 m³ und die CO2-Emissionen um 689 Tonnen pro Jahr gesenkt werden), Photovoltaik und unserem Trigenerationssystem, das mit einem einzigen Gerät gleichzeitig Strom, Wärme und Kälte erzeugt. Durch die Installation von sieben Photovoltaikanlagen auf Gebäuden am Standort seit 2014 konnten wir jährlich 300.000 kWh und 120 Tonnen CO2 einsparen, und wir verbessern kontinuierlich ihre Effizienz.
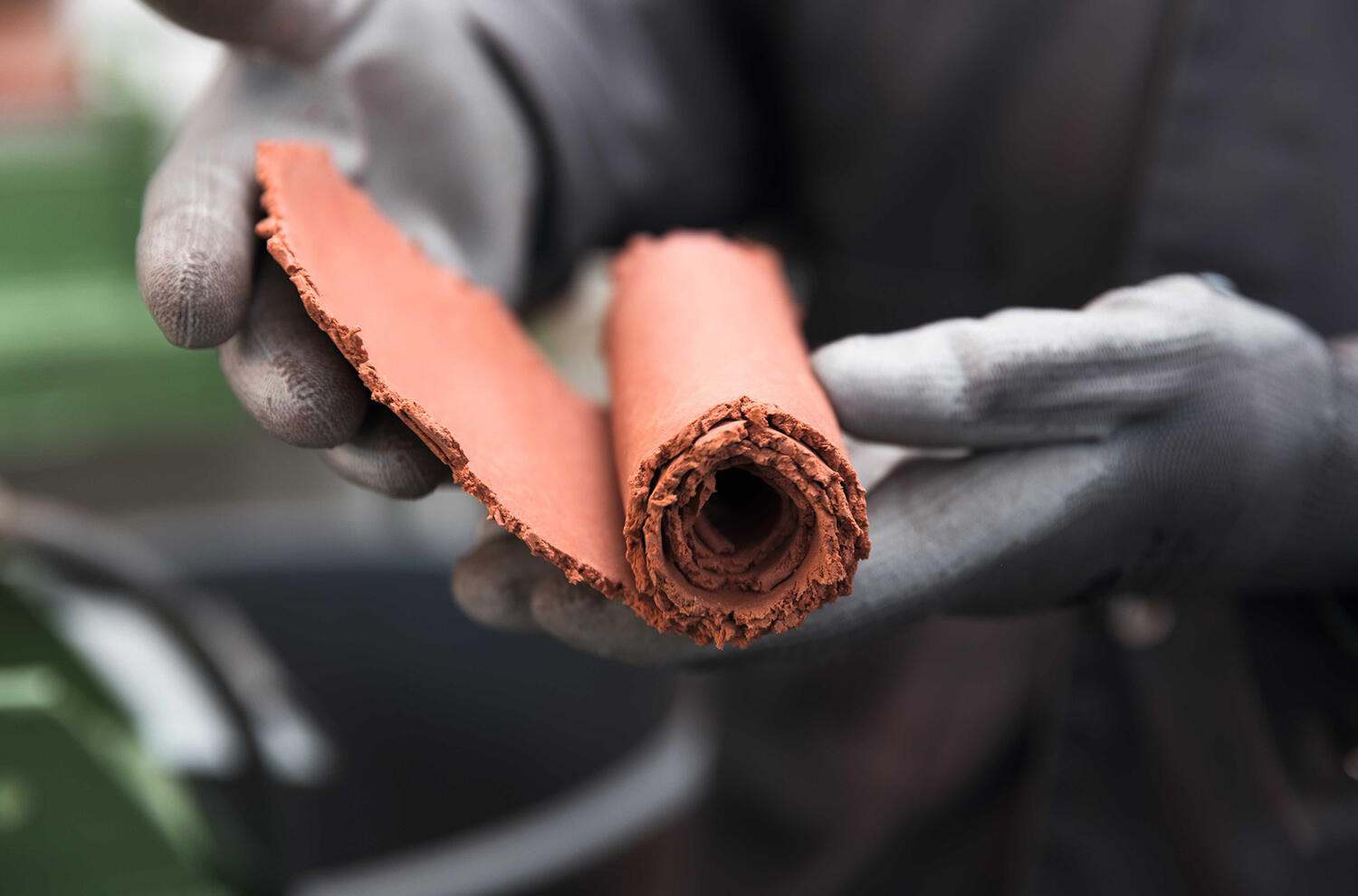
Schritt 3 - Emissionen: Recycling zur Reduzierung unseres ökologischen Fußabdrucks
In Narni recyceln wir jährlich 750 Tonnen Linoleum und liefern damit hochwertige Sekundärrohstoffe für neues Tarkett Linoleum. Wir verwenden 36 % recyceltes Material, darunter 10 % recyceltes Tarkett-Linoleum, sowie recycelten Kork und Holz. Insgesamt hilft uns das Recycling von Linoleum, jährlich 1.194 Tonnen CO2 einzusparen.
Und wir sind immer auf der Suche nach neuen Partnern, um innovative Wege zur Wertschöpfung aus unseren Abfällen zu finden. So verkaufen wir beispielsweise pulverisierte Produktionsabfälle aus unserem Linoleum-Silencio-Sortiment an ein lokales Verpackungsunternehmen, das die Kappen zum Schutz unserer Linoleumrollen während des Transports herstellt und damit einen Beitrag zur Kreislaufwirtschaft leistet.
Wir ermutigen unsere Kunden, uns über das Tarkett ReStart®-Recyclingprogramm Verlegeverschnitt zuzusenden, der bis zu 5 % eines neuen Linoleumbodens ausmachen kann. Narni hat das Linoleum-Recycling durch ReStart® seit 2010 verdoppelt. Wir sind auf dem besten Weg, bis Ende 2020 150 Tonnen zu erreichen. Um diesen Vorgang so CO2-effizient wie möglich zu gestalten, konsolidieren wir den Transport des Recyclingmaterials innerhalb unserer bestehenden Logistikabläufe.
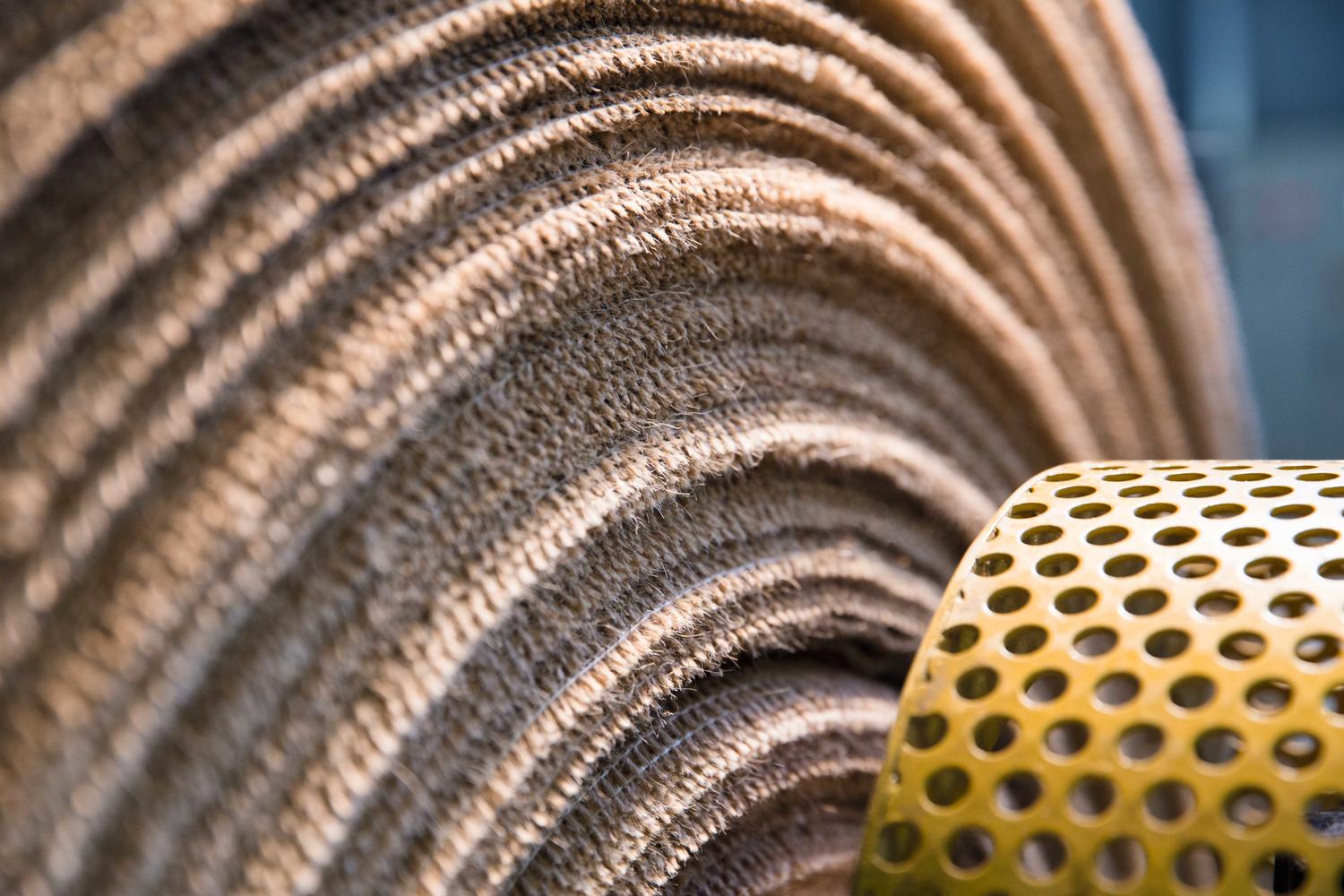
Blick in die Zukunft
Aufbauend auf diesen Erfolgen werden wir unsere Energieeffizienz-Initiativen in Narni ausweiten und sowohl den Wärme- als auch den Stromverbrauch reduzieren, um unsere CO2-Emissionen bis 2030 um weitere 10 % zu senken. Wir werden unsere Kunden weiterhin für die CO2-Reduktion und die Umweltvorteile durch Recycling mit Tarkett ReStart® sensibilisieren. Und schließlich werden wir das Recyclings von gebrauchtem Linoleum weiter ausbauen.